Pressure and Reserve Vessels (Power Plants, Petrochemical, and Refinery Equipment)
The manufactured equipment in AzarAb is mostly from pressure and reserve vessels. Reserve vessels are from aerial and land kinds, which use for reserving water and fuel and industrial material in refineries, power plants, petrochemical plants and other industrial places. Pressure vessels are used in process affairs in industries such as refineries, power plants petrochemical plants, food industries and compressed air industries and even are used as anti-shock in civil water supply systems. These vessels divide into two mobile and stable parts. The mobile ones use for transporting oil, gas, flammable and toxic products. The stable vessels formally divide into vertical and horizontal types that each of them are chosen in regard with the use and the condition of place and other special usage.
Pressure vassals
Pressure Vassals’ General Specifications
Most pressure vessels are in circular or cylindrical shapes in which in cylindrical one, the heads are round, or elliptical produced in hot or Cold rolling.
The pressure vessels, which are manufactured in AzarAb, are as following:
- Drums
- Heat Exchangers
-Towers
- Power Plants Pre-Heaters
- Chemical Reactors
That is used in oil, gas, and power plant industries.
Pressure Vessels Technical Specifications
Planning and manufacturing of pressure vessels are designed based on parameters such as operation pressure, operation thermal temperature, used steel, size, workshop facilities, environmental effects, climatic conditions, lifetime, and friction resistance; as below described:
- Planning standards of vessels pressure such as ASME and BS is related to thickness and raw material authorized stress, welding facilities. Primary calculations will be performed by use of current related planning resources and software.
- Thermal temperature is also too important and has a direct effect with authorized body stress and suggested thickness for the vessel.
- Raw material in pressure vessels is carbon steel or stainless steel, -and in special cases- aluminum, copper and brass; and now a day in direct sea industries titanium in mentioned equipment. Choosing the material is based on ASME, ASTM, BS, and or DIN regarding authorized stress, operation thermal temperature, friction, extruding and welding capabilities.
- Vessel size, which is directly in relation with its diameter and height, normally is assigned according the vessel process and the entering factor in calculating some parameters specially the body thickness and holders resistant calculate
- Environmental parameters (such as wind, earthquake) are considered as additional loads (vertical and horizontal) to vessel in different conditions.
- Final thickness will be planned according the resistance against friction
- All manufacturing procedures such as choosing material, blanching, cutting, mechanical tests, rolling, welding, constructing, and assembling will be controlled by Quality Control and employer inspectors.
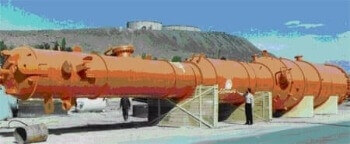
A Sample Tower Designed and Manufactured In Azarab
Planning Standards and Methods:
American standard ASME, British BS5500, and other ones including German and Italian standards are some of standards, but in AzarAb, the American standards such as ASME Sec VIII and Div I. and II. are used more.
Planning and performance drawings would be prepared according the current standards based on the calculations after assigning the resistance parameters such as body thickness, holders dimensions, holders bolts specifications (regarding the number and size), parts engineering specification, welding method and material; with regard to the workshop capabilities and finally the details would be assigned.
PV elite, Aspen B- jack, Nozzle Pro, Compress, Nastran, and Ansys are the software that AzarAb uses in planning pressure vessels. They are updated based on the last global standard changes.
Different joints such as fluid inlet and outlet nozzles, manhole and hand hole and also gates of pressure gouge installs, temperature sensors, liquid gouge, emergency offloading valves, pipe clips, ladders and seats and inner equipment including for absorber, trays, distributors, akeneh holders installed on vessels. Experts of Construction Engineering department monitor all planning and manufacturing details.
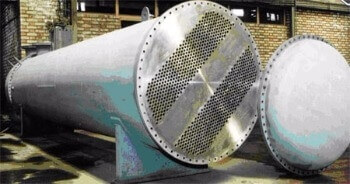
Sample of a Heat Exchanger Designed and Manufactured In Azarab
Performing Final Tests
After finishing the manufacturing processes, products will be tested with pressure water based on hydrostatic standard tests. In order to release stress remained due to forming and welding and so on, the vessel will be put in stress relive furnace for a standard temperature and time. VT, PT, and RT are the final welding tests, which performs by quality control Experts based on employers’ and Design department's views.
Reservoir Vessels:
Fuels and chemical reserves with 300,000ms capacity, 150m diameter and 24m height are manufactured in AzarAb based on API 650 and API 620 Standards.
Recently AzarAb has won and performed such big projects in form of EPC. In EPC projects in addition to performing of the mechanical and metal equipment making other actives such as excavation, foundation, construction monitoring, electricity, and precise tools are included too.
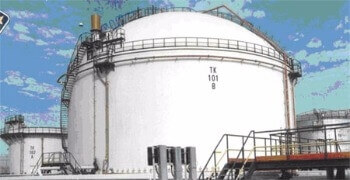